ENGINE TRANSMISSION SYSTEM
INTRODUCTION
A transmission is a machine in a power transmission system, which provides
controlled application of the power. Often the term transmission refers simply
to the gearbox that uses gears and gear trains to provide speed and torque
conversions from a rotating power source to another device.
The term transmission refers to the whole drivetrain,
including clutch, gearbox, prop shaft (for rear-wheel drive), differential, and
final drive shafts. In American English,
however, the term refers more specifically to the gearbox alone, and detailed
usage differs.

Engine transmission system
The most common use is in motor vehicles, where the
transmission adapts the output of the internal combustion engine to the drive
wheels. Such engines need to operate at a relatively high rotational speed,
which is inappropriate for starting, stopping, and slower travel. The
transmission reduces the higher engine speed to the slower wheel speed,
increasing torque in the process. Transmissions are also used on pedal bicycles,
fixed machines, and where different rotational speeds and torques are adapted.
A transmission has multiple gear ratios (or simply
"gears") with the ability to switch between them as speed varies.
This switching may be done manually (by the operator) or automatically.
Directional (forward and reverse) control may also be provided. Single-ratio
transmissions also exist, which simply change the speed and torque (and
sometimes direction) of motor output.
In motor vehicles, the transmission generally is connected
to the engine crankshaft via a flywheel or clutch or fluid coupling, partly
because internal combustion engines cannot run below a particular speed. The
output of the transmission is transmitted via the driveshaft to one or more
differentials, which drives the wheels. While a differential may also provide
gear reduction, its primary purpose is to permit the wheels at either end of an
axle to rotate at different speeds (essential to avoid wheel slippage on turns)
as it changes the direction of rotation.
Conventional gear/belt transmissions are not the only
mechanism for speed/torque adaptation. Alternative mechanisms include torque
converters and power transformation (e.g. diesel-electric transmission and
hydraulic drive system). Hybrid configurations also exist. Automatic
transmissions use a valve body to shift gears using fluid pressures in response
to speed and throttle input.
Requirements Of Transmission System
- Provide means of connection and disconnection of engine with rest of power train without shock and smoothly.
- Provide a varied leverage between the engine and the drive wheels
- Provide means to transfer power in opposite direction.
- Enable power transmission at varied angles and varied lengths.
- Enable speed reduction between engine and the drive wheels in the ratio of 5:1
- Enable diversion of power flow at right angles.
- Provide means to drive the driving wheels at different speeds when required.
- Bear the effect of torque reaction , driving thrust and braking effort effectively.
Types of transmission system
1. Manual transmission
2. Automatic transmission
3. Semi-automatic transmission
4. Continuously-variable transmission (CVT).
How to work in transmission system
1. Manual Transmission system
As the name suggests, the selection of gear ratios on manual transmissions is accomplished by manually shifting a gear selector mechanism that disengages one gear and selects another. Most modern types of this transmissions have five or six forward (and one reverse) gears.
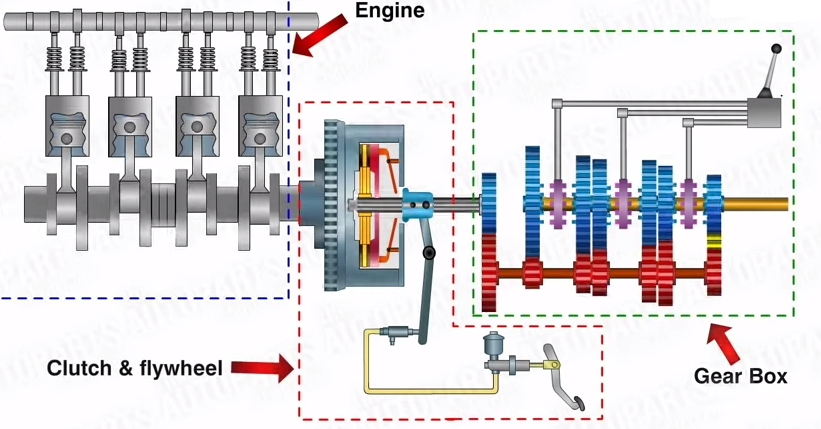
Manual Transmission system
This type of transmission is connected to the engine via a clutch, which if disengaged (by pressing the foot pedal or hand lever), removes torque from the system. With the clutch engaged, power is delivered to the transmission through an input shaft that is separated from the primary cluster, and which can rotate at a different speed to the cluster. The cluster is comprised of gears that can be moved to either engage, or disengage from fixed gears on the secondary shaft, which is normally located below the cluster gears, and supported by roller bearings in its casing.
Gear Selection
The input shaft has only one gear that engages with a gear on the secondary shaft. When it is running and the clutch engaged, the transmission is said to be in “Neutral”. No gears on the primary are engaged with gears on the secondary shaft.
When shifting into first gear (for example), the gear on the primary shaft is slowed down by a synchronisation mechanism, and aligned with a gear on the secondary shaft. The current gear is always disengaged before the next one is engaged. When the clutch is re-engaged, rotational energy is transferred from the transmission to the axle(s) by the drive train.
By using progressively smaller ratios, the speed of the vehicle can be maintained or increased using less power from the engine.
2. Automatic transmission system
In an automatic transmission, the hydraulically operated control systems are managed electronically by the vehicle’s computer instead of the clutch and gear stick. All the driver has to do is shift the selector from Park (P) or Neutral (N), into Drive (D), and the gear shifting will take place automatically and smoothly, without any additional input from the driver under normal driving conditions.
Automatic transmission system
Gear selection
Gear selection in automatic transmissions depends on many operational conditions, such as vehicle speed, engine speed, performance mode (where fitted) selected as well as driver assist systems such as traction control, stability control, automatic/autonomous braking and cruise control.
Provided all necessary conditions are met, and there is agreement between the Engine Management and Transmission Control systems, pressurized transmission fluid is automatically channelled to mechanisms that drive sets of planetary gears and clutches, which are roughly analogous to the gear ratios found in in this type of transmission.
Rotational energy is provided by a torque converter, a mechanism consisting of two freely rotating parts. One half is attached to the engine and the other to the transmission input shaft. The two halves of the converter are positioned very closely together. The fluid that circulates between them is influenced by the rotational energy of the engine which in turn impacts the transmission side of the converter. Torque is transferred from the engine to the transmission thanks to the shearing strength of fluid.
In older automatic transmissions, the shifting action was accomplished by internal fluid pressures overcoming spring tension – closing one circuit before opening another. This control system produced harsh, jerky shifting. Modern systems moderate the action of the controlling valve shuttles, providing almost seamless shifting.
3. Semi-Automatic transmission system
Also known as an “automatic manual” or “clutchless manual” transmission, the simplest way to describe this type is to call it a hybrid between a fully automatic and manual transmission.
Similar to a manual transmission, gears are changed via a simple shifter or paddles located behind the steering wheel. However, there is no need to operate a clutch pedal. Processors, sensors, pneumatics and actuators are all used to “automatically” shift the gears once the drive has signalled the change.
Semi-Automatic Transmission system
The basic principles of shifting mechanical gears in a semi-automatic fashion have been in use on heavy commercial vehicles for many years. The latest and best designs provide lightning-fast, almost undetectable gearshifts.
The design of these systems varies, but all semi-automatic transmissions rely on microprocessors to control the changing of mechanical gear ratios with the help of electrically operated actuators and servos. These transmissions were limited to high-end supercars at first due to their high cost, but an increasing number of manufacturers are fitting them to mid-range cars.
Dual clutch systems employ two clutches, one controlling gearshifts in the even numbered gears and, anther that controls the odd numbered gears and reverse. This arrangement does not interrupt the power flow from the engine. The driver still has to initiate a gearshift via a shifter or paddles located behind the steering wheel, but there is no need for the driver to operate a clutch.
4.Continuously-variable transmission (CVT).
Unlike the others on this page, this transmission doesn’t use gears as its means of producing various vehicle speeds at different engine speeds. Instead of gears, the system relies on a rubber or metal belt running over pulleys that can vary their effective diameters. To keep the belt at its optimum tension, one pulley will increase its effective diameter, while the other decreases its effective diameter by exactly the same amount. This action is exactly analogous to the effect produced when gears of different diameters are engaged.
Continuously-variable transmission
Gear Selection
Since one pulley is driven by the engine and the other is connected to the drive shaft, an infinite number of ratios can be produced. This enables it to always run at the most efficient speed, regardless of the load placed on it. Microprocessor-controlled sensors quantify load variations and by adjusting both pulleys, the optimum operating speed for the engine can be maintained without any input from the driver.
This post will be very useful to us....i like your blog and helpful to me....nice thoughts for your great work..Hydrauliques Continental
ReplyDeletenice
ReplyDeleteVery informative post thanks for sharing it. Find the best Planetary Gearbox Manufacturers in India
ReplyDeleteNice post. Are you looking for the top rolling mill suppliers in India
ReplyDeleteNice Post. Thanks for Sharing
ReplyDeletesuspension parts manufacturers in India
Best Automobile Part Manufacturers in India
Shock Absorber Manufacturers in India
Brake Shoe Manufacturers in India
Brake Manufacturers in India
Car Suspension Parts Manufacturers in India
Universal Joint Cross Manufacturers
Bearing Manufacturers
Brake Shoe Manufacturers